TM 5-4930-244-14
b. Cleaning. (Sheet 2 of 4).
WARNING
·
Dry cleaning solvent is flammable. Do not use near open flame or non-
ventilated places. Keep away from open flames or sparks. Avoid inhaling
solvent fumes. Avoid contact with skin. Flash point of solvent is 100° F to
138° F (38° C to 59° C).
(1)
Clean cylinder barrel (7), piston (6), rod (1), shims (4), and all attaching hardware of all carbon, grease, oil, and
dirt with solvent and rags.
(2)
Remove all carbon deposits from piston (6) and ring grooves (9) with solvent and rags.
(3)
Remove all carbon deposits and other obstructions from small holes (oil ports) in piston (6).
WARNING
Compressed air used for cleaning purposes will not exceed 30 psi. Use only with
effective chip-guarding and personal protective equipment (goggles/faceshield,
gloves, etc ).
(4)
Thoroughly dry all parts using clean rags or compressed air.
c. Inspection. (Sheet 2 of 4).
(1)
Inspect rod (1) and attaching hardware for cracks, breaks, scoring, burring, and general condition. Replace all
unserviceable parts.
(2)
Inspect cylinder barrel (7).
(a)
Inspect cylinder barrel (7) for cracks, breaks, hot spots, elongated holes, and general condition.
(b)
Check cylinder bore (10) wear. If cylinder bore (10) exceeds the maximum allowable limit, of 3 150 inches
(8 0 cm), replace cylinder barrel (7).
(3)
Inspect piston (6).
(a)
Check wrist pin (11) and piston (6) for breaks, cracks, scoring, hot spots, and general condition. Replace
any unserviceable parts
(b)
Check diameter of piston (6). Measure piston (6) at the bottom of skirt (12) across thrust face (13). Piston
diameter should be 3.1459 inches to 3.1449 inches (7.990 cm to 7.988 cm).
(c)
Insert piston (6) into bore (10) with crown (14) toward bottom edge of bore (10) and about 0.5 inch (1.27
cm) from bottom edge.
(d)
Insert new rings (15, 16, 17) one at a time into bore (10). Push each ring (15, 16, 17) against piston crown
(14) to ensure that it is level in the base.
(e)
Withdraw piston (6) far enough to allow ring gap to be measured. Ring gap should be 0 012 inch to 0.017
inch (0.305 mm to 0.432 mm) for the firing ring (15) and compression ring (16), and 0.009 inch to 0.019 inch
(0.229 mm to 0.482 mm) for the oil ring (17).
6-8
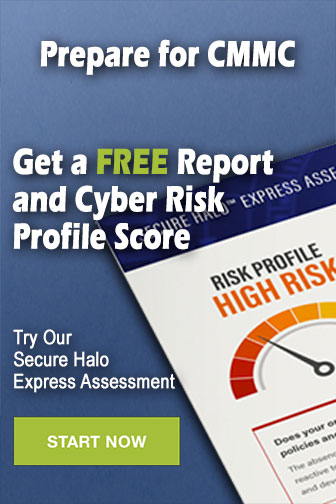