TM 9-4940-568-20
2-219
(c)
Operate all ancillary equipment:
Crane - cycle each crane function two cycles.
(d)
If additional storage time is required, repeat Steps (a) and (b) at yearly intervals.
(5)
Air compressor system extended storage.
To avoid over filling, drain oil before installing additive or damage to equipment may result.
(a)
Drain amount of oil from air compressor crankcase that is equal to the quantity of additive being
added (Para 11-9).
(b)
Add .5 pts VCI-326 (Item 41, Appendix C), vapor corrosion inhibitor or equivalent to air
compressor crankcase.
(c)
Operate to mix additive. Allow pressure to reach 110 psi.
(d)
If additional storage time is required, repeat Steps (a) and (b) at yearly intervals.
(6)
Fuel system extended storage.
(a)
Drain fuel tank.
(b)
Change all fuel filters (Para 8-19).
(c)
Ensure the fuel tank contains at least 20 gallons (75.7L) of treated fuel. The fuel should be treated
with Biobor JF (Item 9, Appendix C), (or equivalent). The addition of 3 teaspoons of Biobor to 20
gallons of fuel will provide adequate protection against fungus growth. When storing in freezing
conditions, the addition of 3 ounces (88.7 ml) of isopropyl alcohol (Item 6, Appendix C), to 20
gallons of diesel fuel will help prevent fuel line freeze up.
(d)
Run engine 5 minutes to circulate clean treated fuel throughout the fuel system.
(e)
All fuel that is added to the FRS during storage must be treated. While in storage, there must
always be at least 20 gallons (75.7L) of treated fuel in FRS fuel tank.
(f)
Cap off fuel system.
(7)
Battery extended storage.
Remove batteries from FRS (Para 3-14) and keep fully charged (TM 9-6150-200-14).
(8)
Check the coolant level (TM 9-4940-568-10). Test the coolant to ensure that the cooling system is
protected against corrosion and temperatures down to 30 degrees F (34 degrees C). Add antifreeze or
corrosion inhibitors compatible with ethylene glycol base antifreeze if cooling system is not adequately
protected (TB 750-651).
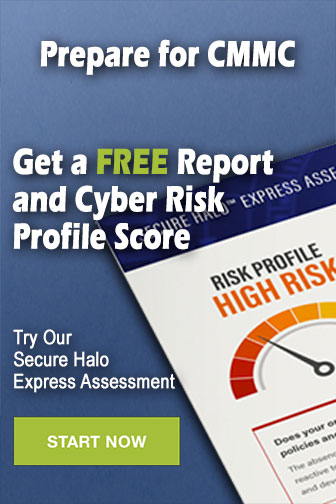