TM 9-2330-238-14
4-11. SPECIFIC
PMCS PROCEDURES.
a.
Organizational
PMCS are provided
in Table 4-1. Always
perform
PMCS in the order listed.
Once it
becomes
a habit, anything that is not right can be spotted in a minute. If anything wrong is discovered
through PMCS,
perform
the appropriate
troubleshooting
task
in Section
IV of this chapter.
If any component
or system
is not
serviceable,
or if given service does not correct the problem,
notify your supervisor.
b.
Before performing
preventive
maintenance,
read all the checks
required for the applicable
interval and
prepare tools needed
to make all the checks.
Have several clean rags (Item 11, Appendix
E) handy. Perform ALL
inspections
at the applicable
interval.
c.
The columns
in Table 4-1 are defined as follows:
(1)
Item No. Provides a logical sequence
for PMCS to be performed
and is used as a source of item
numbers for the TM ITEM NO column
on DA Form 2404 in recording
PMCS results.
(2)
Interval. Specifies
interval at which PMCS is to be performed.
(3)
Item To Be Inspected.
Lists the system
and common
name of items that are to be inspected.
Included
in this column are specific
servicing,
inspection,
replacement,
or adjustment
procedures
to be followed.
(4)
Procedure.
Tells you how to do the required check or service.
Table 4-1. Organizational
Preventive
Maintenance
Checks and Services
(PMCS).
QQUARTERLY
SSEMIANNUAL
AANNUAL
ITEM
INTERVAL
ITEM TO BE
NO.
INSPECTED
PROCEDURES
Q
s
A
1
AIR RESERVOIR
AND AIR LINES
l
Check air reservoir and air lines for damage
and tight connections.
2
WHEELS,
HUBS, AND
BRAKEDRUMS
l
a. Check brakes. Replace
damaged
or worn parts (para 4-38).
l
b.
Rotate
and
match
dual
tires
according
to
degree
of wear
(TM 9-2610-200-14).
3
SPRINGS
AND
SUSPENSION
l
a. Check springs for any evidence
of damage.
l
b. Check for shifted leaves. If evidence of shifting, sagging,
or dam-
age exists, replace
springs (para 4-56).
4-4
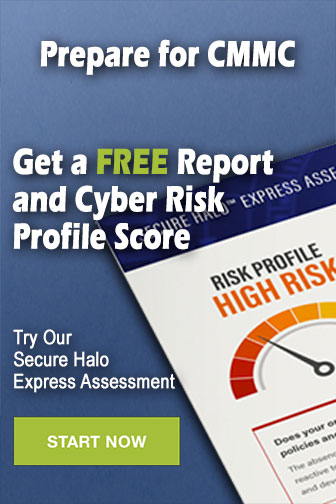