TM 55-8115-203-23 & P
(4) Cut crossmember from side rails with oxygen-acetylene torch.
(5) Grind away excess weld material.
(6) Tack weld replacement crossmember into place.
(7) Continuously weld crossmember to side rails.
(8) Grind away excess weld material which would interfere with seating of floor planks.
(9) Drill new holes through planks and new crossmember. Fill old holes with caulk.
(10) Replace screws.
e. Forklift Test. Test the floor as follows after repair or whenever there is reason to question the structural
soundness of the floor.
(1) Support the empty MILVAN Container on its four corner posts so that all crossmembers are off the ground
at least four inches.
(2) Securely load a 4000 lb (1814 kg) lowmast forklift with a 4000 lb (1814 kg) weight.
(3) Drive the forklift down the center line of the container to the end wall and back out. Drive the forklift
down the right and left sides of the container.
(4) If there is no failure of the flooring or crossmembers, the container is considered acceptable.
3-8. Horizontal and Vertical Slotted Tracks. Cracked or badly distorted horizontal and vertical tracks may cause
failure of the mechanical restraint system under load conditions.
a. Repair of Minor Cracks and Tears.
(1) Grind along length of crack, enlarging crack to ensure full weld penetration.
(2) Continuously weld with oxygen acetylene torch along length of crack until completely filled.
(3) Grind away excess weld metal which might interfere with shoring beam operation.
(4) Paint according to procedure 2-4.
b. Sectioning. If the slotted track is damaged over a section less than half the length of the track, then only the
damaged section should be replaced.
3-35
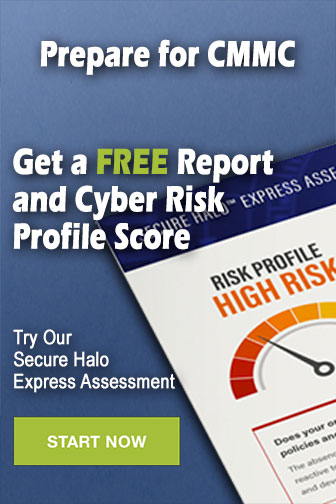