TM 55-8115-203-23 & P
(7)
Drill 1/4 inch diameter holes through the spliced plank sections and the angle support or crossmember.
(8)
Using self-tapping screws, seat screws in position and drive below floor level.
(9)
Apply undercoating according to paragraph 2-4.
d.
Replacement. If it is not possible to splice the plank, replace the plank as follows.
(1)
Unscrew and remove all screws holding down damaged plank.
(2)
Back out screws halfway to loosen adjacent planks.
(3)
Remove damaged plank.
(4)
Remove old caulking and undercoating which may prevent proper seating of new plank.
(5)
Cut replacement plank to fit. Board should fit closely with existing floor on all sides.
(6)
Apply caulking along top of crossmember flange.
(7)
Fit replacement plank in place.
(8)
Drill 1/4 inch diameter holes through the new plank section and the angle support or crossmember.
(9)
Using self-tapping screws, seat screws in position and drive below floor level.
(10)
Apply undercoating according to paragraph 2-4.
(11)
A forklift test as described in paragraph 3-8.e will be applied if, in the judgment of the inspector, any form
of damage exists which might indicate that the container floor is unsound.
2-11. Mechanical Restraint System
a.
Shoring Beam Repair. Repair of the shoring beam consists of straightening the beam. Straighten by mechanical
means only. Do not use heat.
b.
End fitting replacement. Replace end fittings as follows.
(1)
Using a suitable punch, straighten the crimped end of the pin (See fig. 3-13) and drive the retaining pin
from the beam assembly.
(2)
Remove end fitting from beam.
2-21
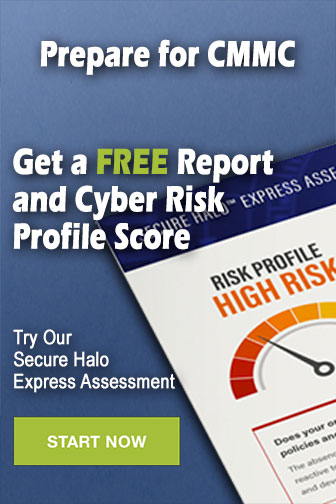