Chapter 1. INTRODUCTIONFigure 1-1. Earth auger, right front view (accoustical panels removed).Figure 1-2. Earth auger, left rear view (accoustical panels installed).Tabulated Data.Figure 1-3. Wiring diagram.Figure 1-4. Hydraulic diagramSection I. SERVICE UPON RECEIPT OF MATERIALFigure 2-2. Auger. bits, and point, removal and installationSection IV. OPERATION UNDER USUAL CONDITIONSFigure 2-3. Controls and instruments.Figure 2-4. Auger operationSection V. OPERATION UNDER UNUSUAL CONDITIONS.Operation in Salt Water AreasChapter III. OPERATOR MAINTENANCE INSTRUCTIONSTable 3-2. TroubleshootingFigure 3-1. Tightening kelly bar (lower) packing UnitCHAPTER IV. ORGANIZATIONAL MAINTENANCE INSTRUCTIONSTable 4-1. Preventive Maintenance Checks and ServicesTable 4-1. Preventive Maintenance Checks and Services - ContinuedTable 4-2. TROUBLESHOOTING ContinuedSection V. TROUBLESHOOTINGFigure 4-1. Radio interference suppression ComponentsFigure 4-2. Radiator, exploded view.Water Pump Drive Belt Adjustment Figure 4-3. Thermostat housing and fan, exploded view.Section VIII. MAINTENANCE OF HYDRAULIC SYSTEMFigure 4-4. Control value, removal and installationFigure 4-5. Hydraulic pump and hoses, removal and installation.Figure 4-6. Hydraulic motor, removal and installation.Figure 4-7. Elevating cylinder, removal and installationFigure 4-8. Elevating cylinder. removal and installationFigure 4-9. Hydraulic reservoir, exploded view.Hydraulic HosesSection IX. MAINTENANCE OF THE FUEL SYSTEMFigure 4-10. Fuel tank, exploded viewFigure 4-11. Alternator. Removal and installation.Figure 4-12. Battery, removal and Installation.Figure 4-13. Instrument panel.Figure 4-14. muffler, and exhaust pipeFigure 4-15. Seat assembly, exploded viewFigure 4-16. Collapsible reel. exploded view.Figure 4 -17. Winch, removal and installation.Figure 4-18. Acoustical panelsSection XV. LUBRICATION DIAGRAMLUBRICATION DIAGRAMREFERENCESAPPENDIX BMODEL IDENTIFICATIONSPECIFICATIONS AND APPLICATION DATARULES OF OPERATIONSERVICE PROCEDURE AND RECOMMENDATIONSTORQUE CONVERTER INSTALLATION DATAPERFORMANCE CHECKPERFORMANCE CHECK - ContinuedOIL FILLER GROUPVALVE CONTROL GROUPVALVE CONTROL GROUP - ContinuedLEFT HAND ASM. CONTROL W/O THROTTLE ARMLEFT HAND ASM. CONTROL W/O THROTTLE ARMOIL LINE GROUPASSEMBLY SHIFT CAPCONVERTER HOUSINGCONVERTER ASSEMBLYCONVERTER ASSEMBLY - ContinuedDRIVE PLATE ASSEMBLYOIL PRESSURE GAUGEOIL LINE ASSEMBLYHEAT EXCHANGER GROUPSHUTTLE ASSEMBLYSHUTTLE ASSEMBLY - ContinuedCLUTCH STACK ASSEMBLYCLUTCH STACK ASSEMBLY - ContinuedOIL FILTER ASM.CASE AND GEAR ASSEMBLYCASE AND GEAR ASSEMBLY - ContinuedCONVERTER ATTACH FITTINGSKITS AVAILABLE FOR 50000 SERIES REVERS-O-MATICINDEXINDEX - ContinuedINDEX - ContinuedREPAIR PARTS AND SPECIAL TOOLS LISTHOW TO USE YOUR PARTS MANUALHOW TO USE YOUR PARTS MANUAL - ContinuedHOW TO USE YOUR PARTS MANUAL - ContinuedGeneral Arrangement/Locator DrawingGeneral Arrangement/Locator Drawing - ContinuedOperaator's Control's/Indicators LocatorControl Valve InstallationControl Vakve Bank AssemblyControl Vakve Bank Assembly - ContinuedCONTROL INSTALLATION-SHUTTLE VALVECONTROL INSTALLATION - SHUTTLE VALVECONTROL INSTALLATION-SHUTTLE VALVECONTROL INSTALLATION-SHUTTLE VALVE - ContinuedINSTRUMENT PANEL ASSEMBLYINSTRUMENT PANEL DECALSINSTRUMENT PANEL DECALSELECTRICAL WIRING INSTALLATIONELECTRICAL WIRING INSTALLATIONENGINE AND TRANSMISSION INSTALLATIONENGINE AND TRANSMISSION INSTALLATIONENGINE AND TRANSMISSION ASSEMBLY/PLUMBINGENGINE AND TRANSMISSION ASSEMBLY/PLUMBINGRADIATOR ASSEMBLYRADIATOR ASSEMBLY - ContinuedMUFFLER AND EXHAUST PIPEMUFFLER W/ALTERATIONDRIVE LINE ASSEMBLYDRIVE LINE ASSEMBLYFUEL RESERVOIR ASSEMBLYFUEL RESERVOIR ASSEMBLY - ContinuedFUEL RESERVOIR PLUMBINGACCOUSTICAL PANEL INSTALLATIONACCOUSTICAL PANEL INSTALLATION - ContinuedDRIVE ASSEMBLY LOCATORFINAL DRIVE ASSEMBLYFINAL DRIVE ASSEMBLY - ContinuedRIGHT ANGLE DRIVE ASSEMBLYRIGHT ANGLE DRIVE ASSEMBLY - ContinuedFEED RAM/POLESETTER LOCATIONFEED RAM ASSEMBLYFEED RAM ASSEMBLY - ContinuedPOLESETTER AND WINCH ASSEMBLYPOLESETTER AND WINCH ASSEMBLY - ContinuedBOOM ASSEMBLYSHEAVE ASSEMBLY (UPPER) - POLESETTERWINCH ASSEMBLY W/ SHAFT EXTENSIONWINCH ASSEMBLY W/ SHAFT EXTENSIONWINCH MOTOR ASSEMBLYWINCH MOTOR ASSEMBLY - ContinuedROLLER ASSEMBLY - WINCHSHEAVE ASSEMBLY (LOWER) - POLESETTERHYDRAULICS/PLUMINGHYDRAULIC RESERVOIR ASSEMBLYHYDRAULIC RESERVOIR ASSEMBLY - ContinuedHYDRAULIC PUMP ASSEMBLYHYDRAULIC PUMP ASSEMBLY - ContinuedHYDRAULIC PLUMBING INSTALLATIONHYDRAULIC PLUMBING INSTALLATION - ContinuedHYDRAULIC PLUMBING INSTALLATION - ContinuedMAIN FRAME COMPONENTS LOCATORLEVELING CYLINDER ASSEMBLYLEVELING CYLINDER ASSEMBLYELEVATING CYLINDER ASSEMBLYELEVATING CYLINDER ASSEMBLYELEVATING CYLINDER ASSEMBLY - ContinuedSUPPORT JACKS ASSEMBLYSEAT ASSEMBLYSEAT ASSEMBLY - ContinuedTOOL BOX INSTALLATIONTOOL BOX INSTALLATION - ContinuedCOLLAPSIBLE REEL ASSEMBLYCOLLAPSIBLE REEL ASSEMBLY - ContinuedMOUNTING HARDWARE/LOCATIONSPECIAL TOOL DESCRIPTIONOPERATOR AND MAINTENANCE INSTRUCTIONSTable of ContentsIntroductionENGINE IDENTIFICATIONPARTS AND SERVICEOperating InstructionsTemperature GaugeSTARTING THE ENGINESTOPPING THE ENGINESPECIAL SITUATIONSSPECIAL SITUATIONS - ContinuedSPECIAL SITUATIONS - ContinuedSPECIAL SITUATIONS - ContinuedMAINTENANCE SCHEDULE AND RECORDMAINTENANCE INSTRUCTIONSChanging Oil and FilterOil QualityAir CleanerAir Cleaner - Oil Bath TypeCOOLING SYSTEMChecking Belt TensionChecking Water LevelCRANKCASE VENTILATION SYSTEMDisposable FilterCarburetor Idle Adjustment PointsDual Advance DistributorBreaker Point Check and AdjustmentBreaker Point AlignmentIgnition Timing MarksSpark Plug GappingVelocity GovernorCylinder Head Tightening SequenceLubricationFor Indefinite PeriodSPECIFICATIONSSPECIFICATIONS - ContinuedSPECIFICATIONS - ContinuedSPECIFICATIONS - ContinuedSPECIFICATIONS - ContinuedDISTRIBUTOR ADVANCE CHARACTERISTICSSPECIFICATIONS - ContinuedTORQUE LIMITS FOR VARIOUS SIZE BOLTSLUBE OIL SPECIFICATIONSINDEXSERVICEIntroductionBasic EngineFIG. 1 Identification DecalFIG 2 Engine AssemblyFIG 5. Placing Steel Ball in Valve Lifter PlungerPOSITIVE CLOSED-TYPE VENTILATION SYSTEMFIG. 8 Checking Timing Chain DeflectionFIG. 10 Checking Push Rod RunoutFIG 14 Checking Valve Spring PressureFIG. 15 Checking Valve Spring SquarenessMAIN AND CONNECTING ROD BEARINGSFIG. 19 Typical Bearing FailuresFIG. 22. Checking Rotor End PlayFIG 25. Checking Valve Seat WidthFIG. 27 Installing and Measuring PlastigageFig. 29 Checking Piston Ring Side ClearanceFIG 30 Checking Valve ClearanceFIG 31. Closed Crankcase Ventilation System ComponentsFIG 34. Removing Valve Stem SealFigure 37. Cylinder Head Bolt Torque SequenceFIG 39. View Looking at Right Side of EngineFIG. 43 Aligning Cylinder Front CoverFIG 46 Checking Camshaft End PlayFIG 47. Core Plugs and Installation Tools - TypicalFIG. 48 200 CID Six Oil Pump Inlet Tube InstalledFIG. 50 Typical Thrust Bearing AlignmentFIG 53 Typical Connecting Rod Side ClearanceFIG 55 200 CID Six Crankshaft and Related PartsFIG. 57 Typical Camshaft Bearing ReplacementFIG 58 Valve Rocker Arm Shaft AssemblyFIG 62 Checking Valve Spring Assembled HeightFIG. 64 Typical Piston, Connecting Rod and Related PartsIgnition SystemFIG. 2 Advance Mechanisms - Dual Advance Distributor with Single DiaphragmFIG. 4. Battery-to-Coil and Starting Ignition Circuit TestSecondary (High Tension) Wires Resistance TestBreaker Point ResistanceFIG. 6. Centrifugal Advance AdjustmentFIG. 12. Adjusting Breaker Point Spring TensionFIG. 14. Filing Spark Plug ElectrodeVACUUM ADVANCE UNITFIG. 17. Breaker Point InspectionFIG. 16. Spark Plug InspectionFIG. 1. Typical Carburetor Identification TagFIG. 2. Fuel Pump - TypicalFuel SystemPRESSURE AND CAPACITY (VOLUME) TESTINGFIG. 4. Fuel Inlet System, Model 1940FIG. 5. Idle System. Model 1940FIG.8. Accelerator Pump SystemFIG. 10. Remove or Install Accelerator Pump AssemblyFIG. 13. Removing the Vacuum Piston AssemblyFIG. 16. Remove or Install Main JetFIG. 19. Throttle Body and Idle Adjustment ScrewsFIG. 24. Holley Single-Barrel CarburetorFIG. 28. Accelerating SystemFIG. 29. Power Fuel SystemCLEANING AND INSPECTIONFIG. 32. Holley Single-Barrel CarburetorINSTALLATIONDESCRIPTION AND OPERATION ALTERNATORFIG. 2. Alternator Charging System AmmeterFIG. 6. Ignition On-Engine Running at Fast IdleFIG. 1. Starting Circuit Positive EngagementFIG. 2. Starting Cranking Circuit TestFIG 6 Field Grounded Circuit TestFIG 7 Starter MountingFIG. 11 Pinion and Ring Gear Wear PatternsFIG 12 Coil AssemblySTARTER TERMINALDESCRIPTION AND OPERATIONFIG. 3 Altitude Compensation AdjustmentREMOVAL AND INSTALLATION - VELOCITY GOVERNORDESCRIPTION AND OPERATIONTHERMOSTAT REPLACEMENTSpecificationsSpecifications - ContinuedSpecifications - ContinuedSpecifications - ContinuedDISTRIBUTOR ADVANCE CHARACTERISTICSTORQUE LIMITS - FOOT-POUNDSPOSITIVE ENGAGEMENT STARTERPARTS LISTINDEXEngine Assemnly - TypicalCylinder Block and Related Parts - Typical Cylinder Block and Related Parts - Typical - ContinuedENGINE PISTON, CONNECTING ROD & RELATED PARTS-TYPICALENGINE CAMSHAFT, GEAR, BEARINGS and RELATED PARTS-TYPICALENGINE CAMSHAFT, GEAR, BEARINGS and RELATED PARTS-TYPICAL - ContinuedENGINE CAMSHAFT, GEAR, BEARINGS and RELATED PARTS-TYPICAL - ContinuedENGINE CRANKSHAFT, FLYWHEEL & RELATED PARTS-TYPICALENGINE CRANKSHAFT, FLYWHEEL & RELATED PARTS-TYPICAL - ContinuedENGINE CRANKSHAFT, FLYWHEEL & RELATED PARTS-TYPICAL - ContinuedENGINE VALVES, PUSH RODS, ROCKER ARM COVER & RELATED PARTS-TYPICALENGINE OIL PUMP & RELATED PARTS-TYPICALENGINE OIL PUMP & RELATED PARTS-TYPICAL - ContinuedENGINE OIL PUMP & RELATED PARTS-TYPICAL - ContinuedENGINE OIL PUMP & RELATED PARTS-TYPICAL - ContinuedENGINE OIL PUMP & RELATED PARTS-TYPICAL - ContinuedENGINE OIL PUMP & RELATED PARTS-TYPICAL - ContinuedENGINE OIL PUMP & RELATED PARTS-TYPICAL - ContinuedSTARTER and DRIVE ASSY. - POSITIVE ENGAGEMENTSTARTER and DRIVE ASSY. - POSITIVE ENGAGEMENT - ContinuedDISTRIBUTOR-TYPICALDISTRIBUTOR-TYPICAL - ContinuedSUPPLEMENTAL OPERATING, MAINTENANCE AND REPAIR PARTS INSTRUCTIONSTABLE OF CONTENTSTABLE OF CONTENTS - ContinuedINTRODUCTIONMAINTENANCE SUPPORT DATAMAINTENANCE SUPPORT DATA - ContinuedPROCUREMENT STATUSREPAIR PARTS AND SUPPORTPERSONNEL AND TRAININGEQUIPMENT PUBLICATIONSWARRANTYWARRANTY - ContinuedBASIC ISSUE ITEM LIST (BILL)MAINTENANCE ALLOCATION CHARTColumn Entries Used in the MACSECTION II - ASSIGNMENT OF MAINTENANCE FUNCTIONSSECTION II - ASSIGNMENT OF MAINTENANCE FUNCTIONS - ContinuedSECTION II - ASSIGNMENT OF MAINTENANCE FUNCTIONS - ContinuedSECTION II - ASSIGNMENT OF MAINTENANCE FUNCTIONS - ContinuedSECTION II - ASSIGNMENT OF MAINTENANCE FUNCTIONS - ContinuedSECTION II - ASSIGNMENT OF MAINTENANCE FUNCTIONS - ContinuedSPECIAL TOOL AND SPECIAL TEST EQUIPMENT REQUIREMENTSMAINTENANCE ALLOCATION CHARTMAINTENANCE ALLOCATION CHART - ContinuedMAINTENANCE ALLOCATION CHART - ContinuedDSS PROJECT CODESDA FORM 2765 PART NUMBER REQUESTSAMPLE FORMAT - MILSTRIP REQUISITION FOR CCE (NSN)SAMPLE FORMAT - MILSTRIP REQUISITION FOR CCE (NON-NSN)SAMPLE FORMAT - MILSTRIP REQUISITION FOR CCE (NON-NSN) - ContinuedSAMPLE FORMAT - MILSTRIP REQUISITION FOR CCE (NON-NSN) (MANUAL)SAMPLE FORMAT - MILSTRIP REQUISITION FOR CCE (NON-NSN) (MANUAL) - ContinuedBASIC ISSUE ITEMS LISTCCE MANUFACTURER FIELD CAMPAIGNS AND MODIFICATION PROCEDURESAPPENDIX HFLOW OF REQUISITIONS AND MATERIEL CCE PARTS (NSN)FLOW OF REQUISITIONS AND MATERIEL CCE PARTS (NON-NSN)MAINTENANCE AND OPERATING SUPPLY LIST (CCE)
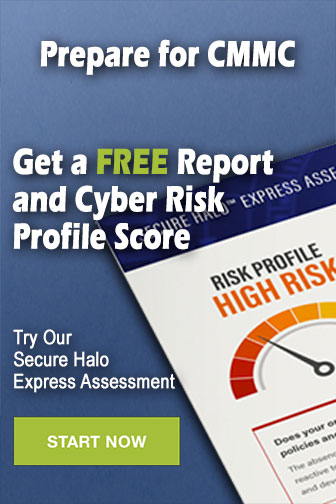